Unfortunately, we soon got the complaint that the injection molded parts are damaged, which obviously made during transportation. Customers' options have always been valued to us, and we react promptly and positively.
Contact the customer to make clear the deadline. We were told that parts are needed to complete the functional test for prototypes.
Remake all the damaged parts. To ease the impact on the progress of customers' product development, we decided to remake all damaged parts. All expenses in production and logistics are covered by RPWORLD.
Contact the insurance company and submit a claim to insurer for the damaged parts. In general, we purchase insurance for each shipment. However, the insurance company is unwilling to take evidence on site because of the COVID-19, so the sum insured has yet to be paid. There is no hesitation when we covered all expenses in advance.
After a few weeks, the customer received the new parts again, and were satisfied with the parts as well as our rapid and all-around service. Soon we received the long and positive feedback from customer, they even recommended us to other companies. Meanwhile, we would like to take this opportunity to express our appreciation for the customer's continued support and positive comment, which always been our motivation.
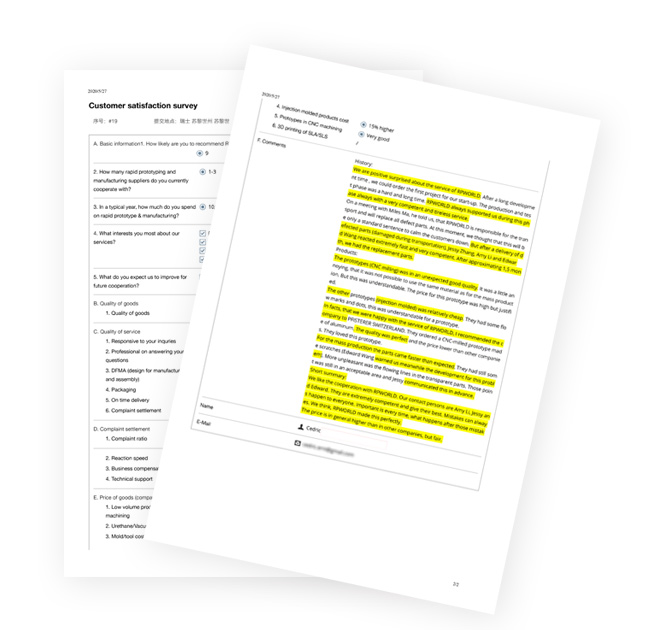
We are positive surprised about the service of RPWORLD. The production and test phase were a hard and long time. RPWORLD always supported us during this phase always with a very competent and tireless service. RPWORLD told us that they will be responsible for the transport and replace all defect parts. At this moment, we thought that this will be only a standard sentence to calm the customers down. But after a delivery of defected parts (damaged during transportation), Jessy Zhang, Amy Li and Edward Wang reacted extremely fast and very competent. After approximating 1.5 month, we had the replacement parts. We realize they are indeed "over promise under deliver".
I recommended RPWORLD to other company. They ordered a CNC-milled prototype made of aluminum. The quality was perfect and the price lower than other companies. They loved this prototype. For the mass production the parts came faster than expected. Edward and Jessy communicated all possible problems in advance. Mistakes can always happen to everyone. Important is every time, what happens after those mistakes. We think, RPWORLD made this perfectly. The price is in general higher than in other companies, but fair.
— Cedric