Are you developing a prototype or mechanical part that features flat surfaces? Although your designs may appear flat, post-production warping can significantly affect prototype validation and part assembly. If your machined part has flat surface, there’re a few things you should be aware of before frozen the part design.
1. What is Flatness for CNC Machined Parts?
“Flatness” refers to the measurement of surface smoothness and uniformity. It dictates that the flat sections of a component should fit between two parallel planes without protruding. It’s one of the crucial factors for assessing the surface quality of a part, particularly in terms of how it affects the fit and fastening performance of mating components. For instance, in precision scientific instrument components, even minor deviations in flatness can lead to significant assembly challenges.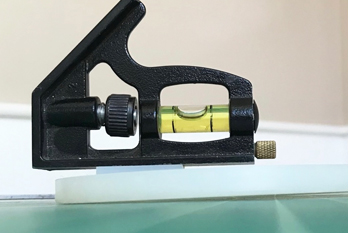
2. What Factors Influence the Flatness of CNC Machined Parts?
Machined surfaces are typically very flat. However, warping can occur due to internal material stress or clamping forces during machining. It’s worth noting that the hardest materials aren’t always the most stable. In some cases, even the toughest materials, such as aluminum and steel, are more vulnerable to bend. Various factors contribute to warpage, including:
● Raw Material: Material type and inherent flatness affects stress and flatness.
● CNC Machine: Precision and condition of the machine impact results.
● Machining Programs and Operator Practices: Program accuracy and operator skill matter.
● Fixturing: Clamping and holding methods can induce stress, leading to warping.
● Material Stress Relief: Proper stress relief techniques prevent warping.
3. How to Ensure Flatness Within Your Requirements?
The degree of warpage in a part is the measured deviation of surface height from the datum plane. The table below helps you select the right flatness tolerances by demonstrating typical ranges for CNC machined parts.
An important consideration in CNC Machining is that achieving a flatter surface requires higher precision for machining, which consequently leads to increased production costs.
At RPWORLD, we work with a wide range of materials with varying degrees of stability and strive to ensure that flatness tolerances meet your requirements. Take the aluminum for instance, which have relatively large coefficient of thermal expansion. We take several measures to prevent warping when machining thin-wall and thin-sheet components. These measures include:
● Eliminate material internal stresses
● Machine symmetrically
● Machine both sides multiple times
● Choose the appropriate cutting tools
● Improve precision of cutting tool
● Prefer new cutting tools
● Combine the rough machining and finish machining
● Select optimal clamping scheme
● Drill before milling
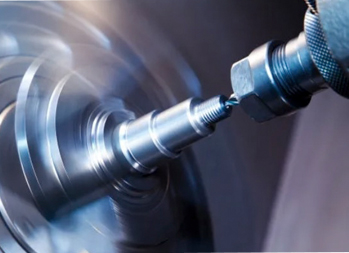
4. How to Measure the Flatness of CNC Machined Parts?
Probing and optical methods serve as the primary means of measuring flatness. Both methods help detect surface irregularities and ensure parts meet specified tolerance levels, thereby avoiding defects and maintaining high manufacturing standards.
Common Instruments for Measuring Flatness:
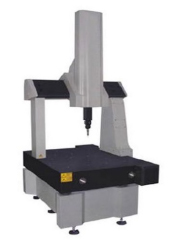
(a) Coordinate Measuring Machine (CMM)
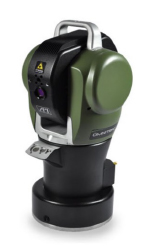
(b) Line Structured Light Scanner
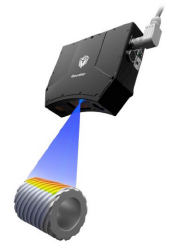
(c) Laser Scanning
5. Why Choose RPWORLD for Precision Flatness in CNC Machining?
● State-of-the-art Equipment for Flatness Measurement:
RPWORLD uses advanced CMM (Coordinate Measuring Machine) and feeler gauge solution to inspect flatness, ensuring product accuracy.
RPWORLD uses advanced CMM (Coordinate Measuring Machine) and feeler gauge solution to inspect flatness, ensuring product accuracy.
● Optimized Tolerance Ranges for Specific Products:
Instead of pursuing the absolute minimum tolerance, we create a cost versus tolerance reduction chart to identify the values that align with acceptable range for a part. This helps choose the tight tolerance that fits your project budget.
Instead of pursuing the absolute minimum tolerance, we create a cost versus tolerance reduction chart to identify the values that align with acceptable range for a part. This helps choose the tight tolerance that fits your project budget.
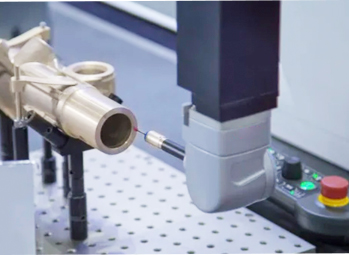
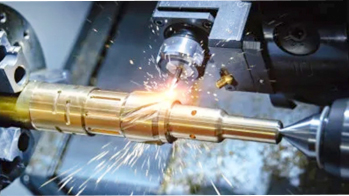
● Advanced CNC Machines: We utilize state-of-the-art 3-axis, 4-axis, and 5-axis CNC milling and turning machines to achieve the machining consistency and ensure that flatness tolerances meet your requirements.
● Rich Expertise: With 20 years of experience in machining over 100 materials, we know how to eliminate material stress effectively to meet your flatness requirements.
● High-performance Engineering Materials: With a reliable sourcing channel, we stock 100+ high-performance engineering materials, ensuring superior flatness, overall consistency, and quality in our CNC machined parts.
Partner with RPWORLD for precision CNC machining that meets your exact flatness requirements. Contact Us and kick off your next project today.