According to a recent research report, the global automotive lightweight materials market is expected to grow 7.3% CAGR from 2023 to 2029. It is expected to reach above $1331.41 Billion by 2029 from $74.79 Billion in 2022. Lightweighting materials play a crucial role in offering the potential for improved fuel efficiency, enhanced performance, and reduced emissions in the automotive industry. It is anticipated that the lighter and more efficient automotive materials and components will revolutionize the industry in the coming years.
5 Types of Lightweight Materials for Automotive Applications
By exploring the various types of lightweight materials used in the automotive sector and their applications, we can uncover their significant contributions to achieving the goals of weight reduction and overall vehicle efficiency.
1. High-Strength Steel
High-strength steel is produced by adding a small amount of alloying elements to ordinary carbon steel. The higher the strength of the steel, the better the weight reduction effect. Although the production cost of this steel is similar to that of ordinary carbon steel, the strengthening effect of the alloying elements significantly increases its tensile strength compared to regular steel. Currently, high-strength steel is mainly used in automotive safety components, chassis, and body structures.

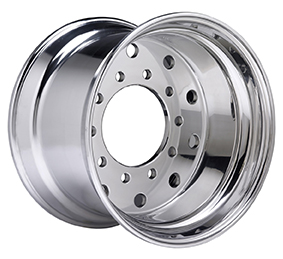
2. Aluminum Alloy
Aluminum is the primary competitor to steel in the automotive body application. The major advantage of aluminum alloy over steel lies in its superior extrusion forming capability, allowing for a weight reduction of approximately 50% when substituting aluminum alloy body panels for steel ones. Currently, numerous automobile manufacturers are demonstrating the potential application of aluminum alloy in automotive lightweighting through the development of aluminum-intensive concept cars. In the automotive industry, around 80% of aluminum alloy is utilized for die-cast components, primarily in areas such as engines, wheels, and other parts.
3. Magnesium Alloy
Magnesium is lighter than aluminum, with a density of only 2/3 of aluminum. Magnesium alloy materials used in automobiles are mainly cast magnesium alloys, accounting for over 90% of the magnesium used in automobiles. Although the proportion of magnesium alloys in current automotive materials is less than 1%, the application of magnesium alloys is receiving attention from major automotive manufacturers worldwide, driven by lightweighting efforts. Taking the United States as an example, the amount of magnesium alloy used in some vehicle models ranges from 5.8 to 26.3 kg per vehicle. In Europe, the amount of magnesium alloy used is second only to North America, with some vehicle models using 9.3 to 20.3 kg of magnesium alloy per vehicle.
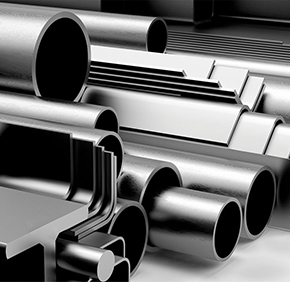
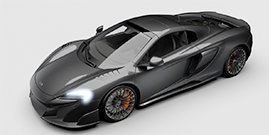
The figure shows Lamborghini Gallardo LP 570-4 SuperLeggera, which extensively utilizes carbon fiber materials in its body and interior. It is the lightest among Lamborghini's available models.
4. Carbon Fiber
Carbon fiber is a fibrous composite material with a carbon content exceeding 90%. It possesses the inherent characteristics of carbon materials while also exhibiting the softness and processability of textile fibers. It is a new generation of reinforced fiber. It has higher strength than steel and lower density than titanium, making it excellent in electrical, thermal, and mechanical properties. Carbon fiber reinforced composites have sufficient strength and stiffness, making them the lightest materials for manufacturing major structural components of automobiles, such as car bodies and chassis. It is estimated that the application of carbon fiber composite materials can reduce the weight of automobile bodies and chassis by 40% to 60%.
5. Modified Plastics
Through methods such as filling, blending, and reinforcement to improve the flame retardancy, strength, impact resistance, toughness, and other performance, based on general plastics and engineering plastics, we got modified plastics. Currently, they are mainly used in exterior trim parts, interior trim parts, and functional and structural components in the automotive industry. The main varieties of plastics are shown in the diagram below:
At a Glance: The Comparison of Lightweight Materials
In terms of weight reduction, the materials currently used for automotive lightweighting show an increasing trend in effectiveness: high-strength steel, aluminum alloy, magnesium alloy, and carbon fiber. However, from a cost perspective, these materials exhibit an increasing trend in terms of cost: high-strength steel, aluminum alloy, magnesium alloy, and carbon fiber.
The comparison of different lightweight materials for automotive applications.
Of course, there are indeed many ways to move to the lighter weight automotive components and products. The good news is that RPWORLD can offer rapid prototyping and low-volume production services, along with in-house expertise and different materials. You have a wide variety of resources at RPWORLD to help you in reducing the weight of car components.
If you have any inquiries or concerns regarding automotive materials, manufacturing processes, or design, please feel free to Contact Us.