Electromagnetic compatibility (EMC) refers to the ability of a technical device not to interfere, or to be interfered, by other devices from unwanted electrical or electromagnetic effects. Controlling electromagnetic interference (EMI) and minimizing electromagnetic susceptibility (EMS) are two important aspects to ensure EMC at a specified level and under specific operating conditions in almost all electronic systems, especially medical devices and scientific instruments.
Common EMC Standard(s) in Different Applications 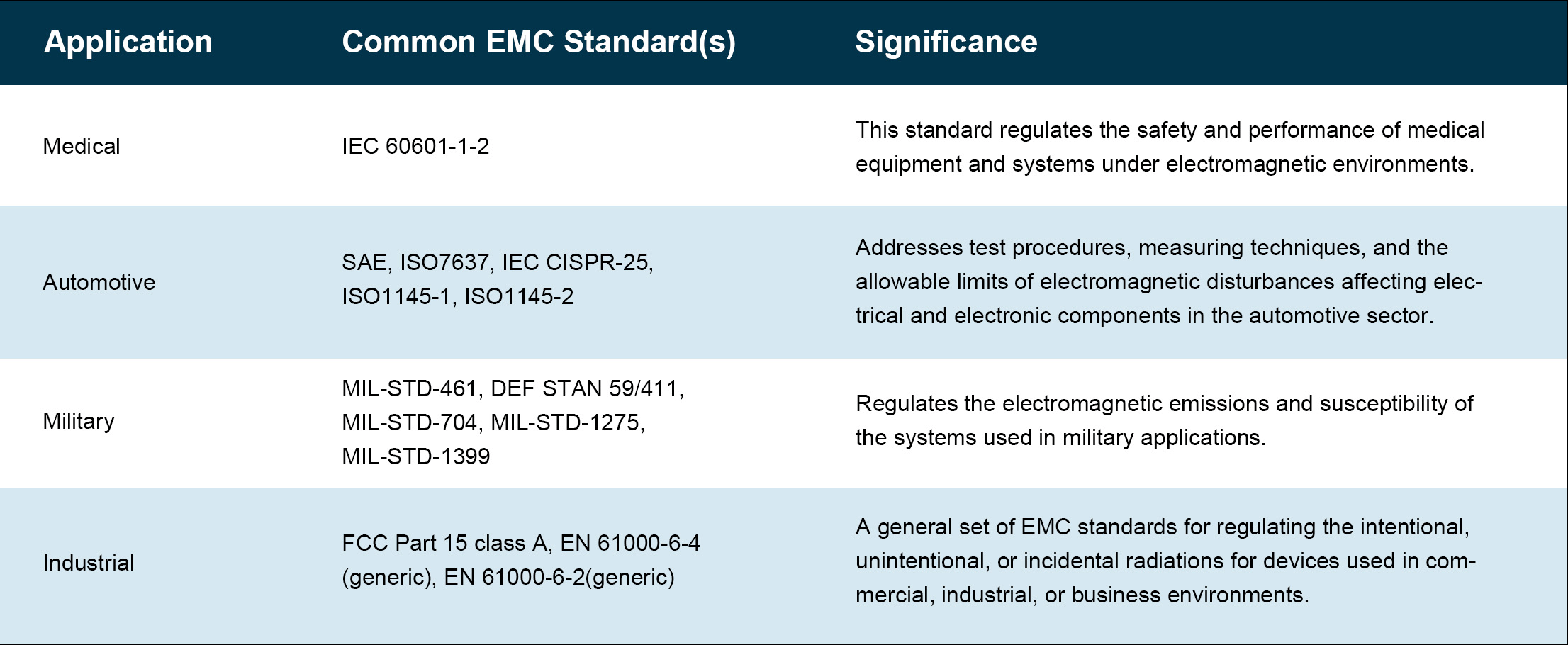
EMC Coating
When it comes to scientific instruments, most of which are precision equipment, the reliability and stability of electronic systems are highly required. While for medical devices, it is vitally important and potentially life-saving to prevent Electromagnetic Interference (EMI) with reasonable design. There’re several ways to make the components less vulnerable to EMI effects, and achieve EMC:
- ● Choose the stable electric components
- ● Design the reasonable circuit, such as minimizing the rate of change of current, or connecting the ground planes.
- ● Design enclosures with signal shielding functions, such as use plastic material with conductive coating.
The plastic enclosures are widely used in lab equipment and medical devices due to its flexible, light-weight and insulative properties. Given the fact that plastics provide no shielding unless the conductive paint is coated, the conductive copper coating is preferred to achieve EMC coating thanks to its availability, cost, durability, and ease of application. However, the plastic enclosure must be properly designed, such as reducing the openings, pasting the conductive tape, etc.
How RPWORLD Manufacturing Helps Achieve EMC and More?
RPWORLD on-demand manufacturing solutions enable your plastic enclosures to achieve EMC and realize light dispersion on specific area of part surface, without affecting cosmetic appearance.
RPWORLD Manufacturing Solutions — EMC Coating
● The painted appearance surface meets requirement of corrosion and wear resistance.
● The internal surface is coated with conductive copper and different paints to achieve EMC. The thread holes and specific grooves are avoided when painting.
● Copper coating can be further processed to meet the need of light dispersion.
● Have the painted surface cross-cut tested, and testing report can be provided.
Typical Properties of RPWORLD Copper Paint
The figure below shows the performance parameters of RPWORLD copper paint. The parameters differ in specific applications: the curved surface and flat surface are different; Part details like ribs and clips cause the thinner copper paint, further affecting the performance. You are suggested to contact us for expert suggestions.
Effectiveness of Different Conductive Coating Shields
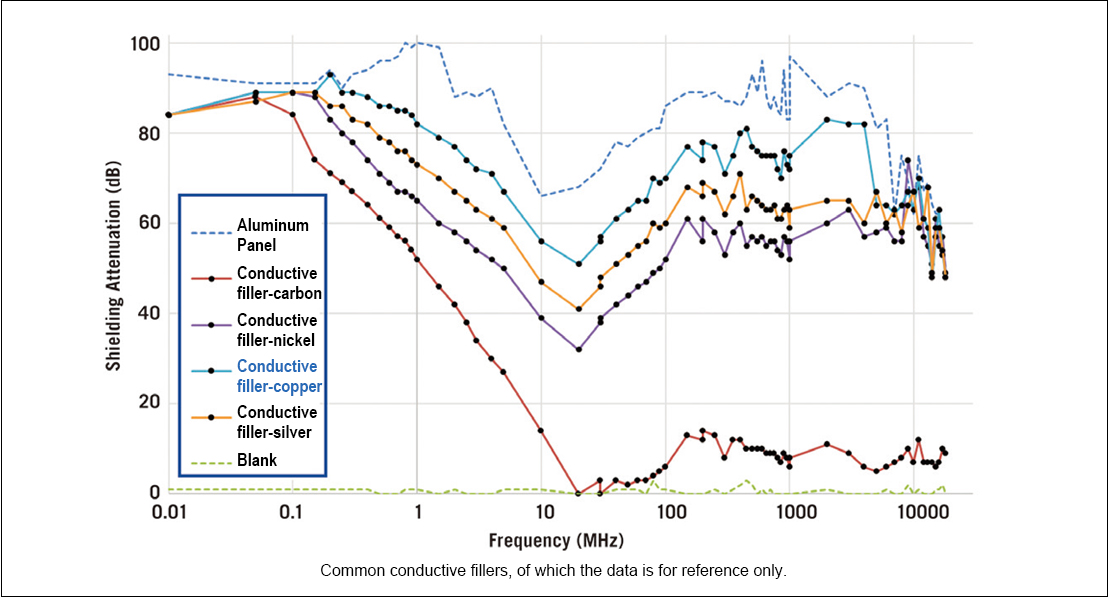
Trusted by Renowned Companies
Why RPWORLD Manufacturing Services
If your project is featured with the following,
contact RPWORLD to accelerate the development:
● Lab equipment
● Any equipment or devices with EMC requirement
● Complex-geometry plastic enclosures
● R&D project with EMC requirement
● Immature circuit design under R&D phase
ISO 9001:2015 certified
Provide resistance & adhesion force test
One-stop surface treatment solution
(painting, powder coating, printing, anodizing, etc.)
20 years manufacturing experience
of mechanical parts
Free and in-depth DFM analysis
The stringent quality control combining with
advanced inspection equipment